Wake up and smell the rubber
The world market for industrial rubber conveyor belts is being inundated by rapidly growing levels of imports from Southeast Asia, primarily China. Over the past two decades, Chinese exports of manufactured goods have increased twenty-five-fold, with more and more of the manufacturing base in Europe succumbing to this growing dominance. Conveyor belt manufacturing is no exception. Low-grade, cut-price belting imported from Southeast Asia continues to grow at an unprecedented rate. As a result, more and more European belt manufacturers have either gone out of business or have had to reduce capacity by closing production plants
Why is this happening? The attraction is simply a question of price. What are claimed to be ‘like for like’ specification belts manufactured in Asia are being sold at ultra-low prices that are usually at least 50% lower than the belts manufactured elsewhere, especially in Europe. Users of conveyor belts are finding it increasingly difficult to resist the temptation of this level of apparent saving. All too often, conveyor belts are being seen as a commodity rather than the crucially important and highly complex technical component that they actually are. In line with this growing perception has been a corresponding decline in life cycle, reliability and a parallel decline in the level of expectation amongst end-users. Next to this valuable technic
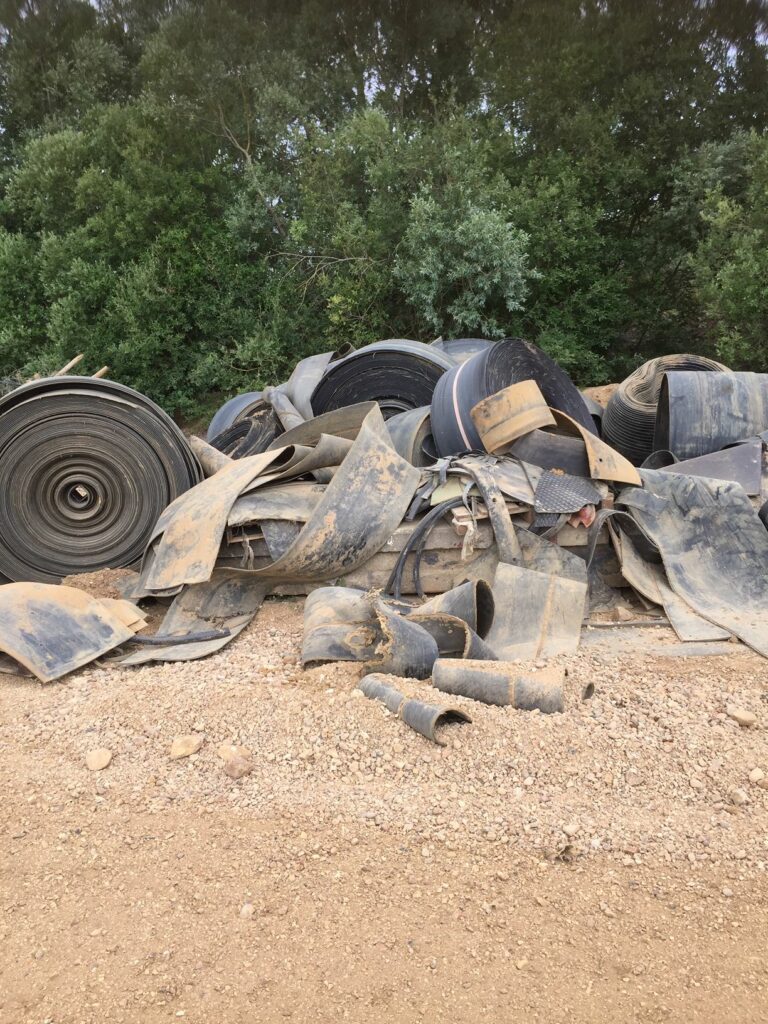
al support and advice is missing in this business segment.
How do Asian manufacturers achieve such low prices? The answer to this question is also easy to explain. The most important factor to bear in mind is that raw materials constitute between 50 to 75% of the total cost of producing a conveyor belt. Rubber Polymers are the biggest part of that cost, so it is the biggest opportunity to cut costs and gain a substantial price advantage. Nearly all conveyor belt rubber is synthetic. Dozens of chemical components and polymers are used to create it so that it is able to cope with the many demands placed upon them. These chemicals and polymers are costly so using low-grade, unregulated versions at the absolute minimum levels, or in some cases not using them at all, is integral to the manufacturer’s ‘lowest sales price’ objective.
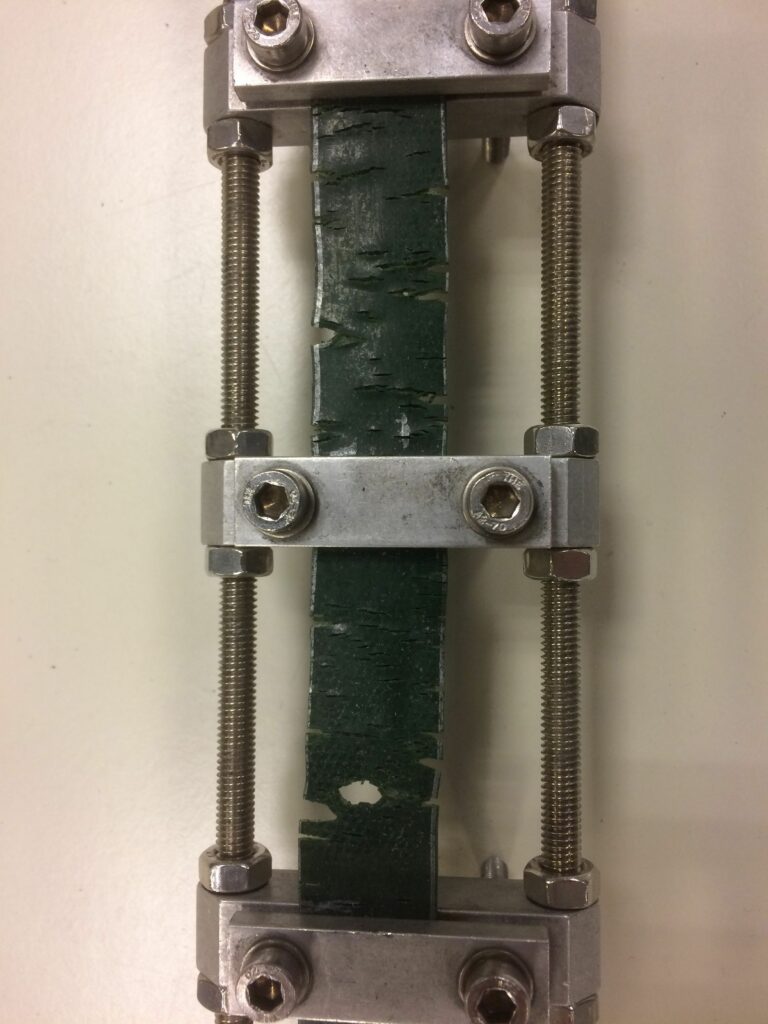
For example, at least 90% of belts imported from Asia are not resistant to the life-shortening effects of ozone and ultraviolet degradation because of the omission for cost reasons of essential antioxidants in the rubber compound. Add to this the use of low grade, all polyester inner fabric plies rather than the more resilient polyester/nylon mix (EP) because nylon is 30% more expensive than polyester. These practices are why the first ‘warning sign’ of an abrasion resistant belt that is not abrasion resistant; an oil-resistant belt that is not oil resistant or a fire-resistant belt that burns like paper is the price itself.
How can I tell the difference between a low-grade belt and a good quality one? In most cases, you can literally smell the difference. Apart from one or two exceptions such as some specialist heat- or fire- resistant belts, good quality rubber emits little or no smell. The smell should be comparable to what you experience in a tire shops. However, a strong, pungent odour is invariably a sign that the rubber is very poor quality and, in some cases, potentially hazardous and environmentally unfriendly.
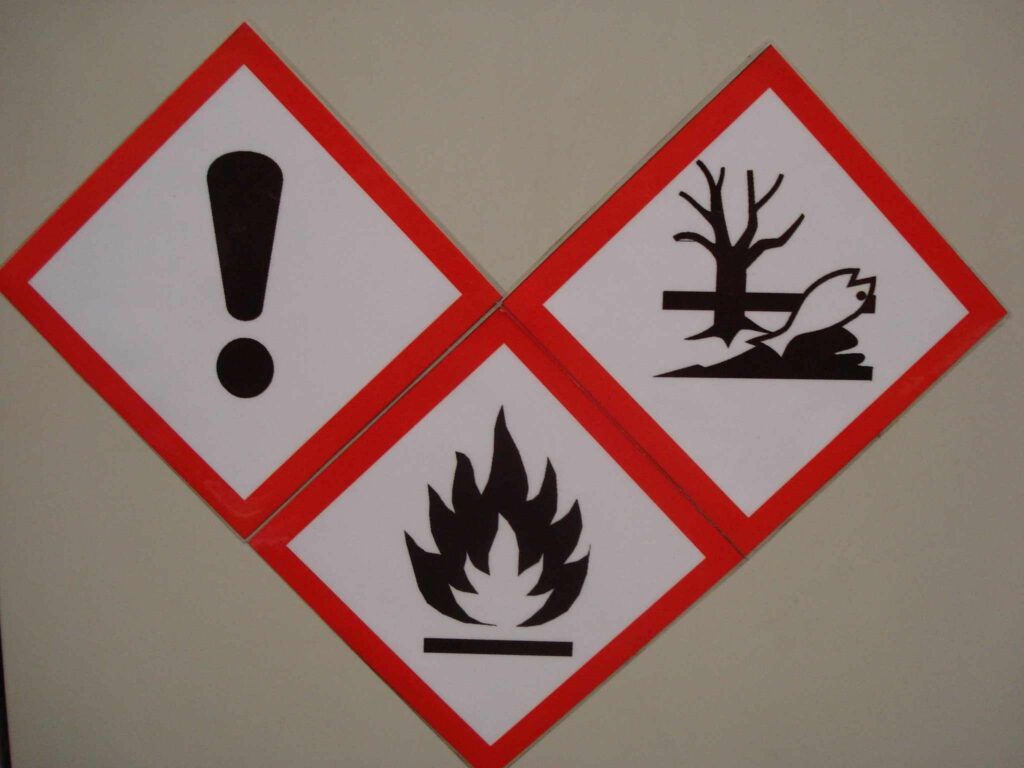
One of the key points to remember is that manufacturers located outside of EU/EEA member states are not subject to European REACH (Registration, Evaluation and Authorisation of Chemical substances) regulation EC 1907/2006 and EU Regulation No. 2019/1021 concerning the use of persistent organic pollutants (POPs). They are therefore free to use much cheaper unregulated raw materials, even though they may be entirely prohibited or have strict usage limitations within Europe.
One of the most contentious issues involves the use of short-chain chlorinated paraffin’s (SCCP’s). REACH regulations stipulate that SCCP’s should either not be used at all or at least only used on a very restricted basis because of their category 2 carcinogenic classifications. Because they pose a threat to the environment they are also subject to POPs regulation. They are most commonly used in Asia. Their presence is a significant contributor to the smell of poor quality rubber.
Another source of the odour is where a high proportion of recycled rubber of questionable origin has been used to reduce the cost of the rubber compound. The more and lower quality recycled content then the greater the smell and the higher a chance of the emission of dangerous VOC (volatile organic compounds).
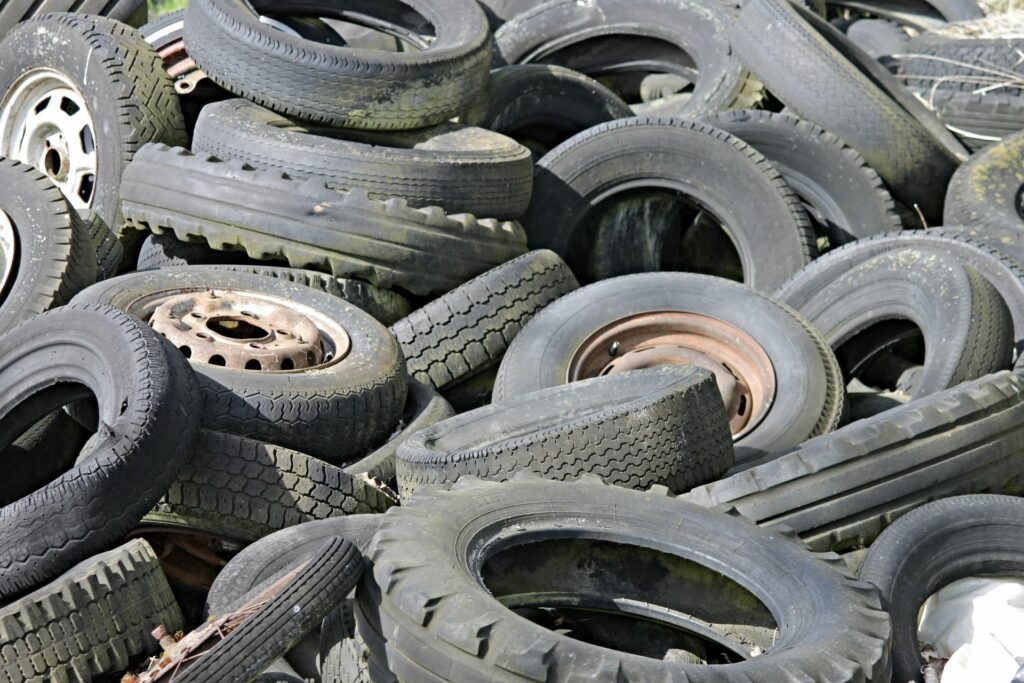
If you ever visit a trade fair where conveyor belts are present then it is very easy to pinpoint the stands where poor quality, imported belts are on display. And anyone involved in conveyor belts who has carried a piece of rubber belt in the back of their vehicle will testify to the fact that it is a smell that lingers for a very long time after the offending piece of belt has been removed!
Conclusion: What is happening has several very serious consequences that impact, both in the short and the long-term, not only the European conveyor belting industry but also the users of industrial conveyor belts in Europe. It’s time to wake up and smell the rubber!
Leslie David